Сплющенный грат что это такое?
Качество стыковой сварки труб ПНД
Бывает так, что во время стыковой сварки труб ПНД качество соединений оставляет желать лучшего. Конечно, в большинстве случаев это зависит от качества монтируемых труб, но бывают случаи, когда причина брака в неверной настройке стыкового сварочного аппарата или неверных действиях персонала.
Давайте разберем, причины возникновения брака при монтаже и способы их устранения.
Параметры качественной стыковой сварки труб ПНД
Для начала, оговорим, какое соединение полиэтиленовых труб можно считать качественным и надежным. Параметры качественной стыковой сварки труб описаны в ГОСТ Р 55276-2012 (ИСО 21307-2011).
Внешний вид сварных соединений, выполненных сваркой нагретым инструментом встык, должен отвечать следующим требованиям:
- валики сварного шва должны быть симметрично и равномерно распределены по окружности сваренных труб;
- цвет валиков должен быть одного цвета с трубой и не иметь трещин, пор, инородных включений;
- симметричность шва (отношение ширины наружных валиков грата к общей ширине грата) должна быть в пределах 0,3-0,7 в любой точке шва. При сварке труб с соединительными деталями это отношение допускается в пределах 0,2-0,8;
- смещение наружных кромок свариваемых заготовок не должно превышать 10 % от толщины стенки трубы (детали);
- впадина между валиками грата (линия сплавления наружных поверхностей валиков грата) не должна находиться ниже наружной поверхности труб (деталей);
- угол излома сваренных труб или трубы и соединительной детали не должен превышать 5°
Размеры валиков наружного грата швов зависят от толщины стенки свариваемых труб (деталей) и должны соответствовать следующим параметрам.
Брак при монтаже полиэтиленовых труб и причина его возникновения.
Маленький грат округлой формы. Причин такого соединения труб может быть две — слишком короткое время нагрева торцов свариваемых труб, либо недостаточное давление при осадке шва.
Чтобы устранить этот вид брака, необходимо произвести заново расчеты сварочного давления и времени остывания и нагрева, согласно сварочной таблице, которая как правило прилагается к аппарату.
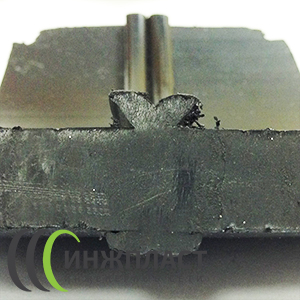
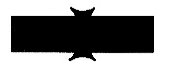
Перекос сварных швов. Причина данного вида брака кроется в некачественной центровке свариваемых труб в станине аппарата, необходимо заново выровнять трубы относительно друг друга.
Максимальная несоосность труб не должна превышать 10% от толщины стенки трубы.
Сварной шов с многочисленными раковинами, возможными следами растрескивания по всему периметру.
Температура нагревательного зеркала слишком высокая, полиэтилен не плавится, а закипает.
Необходимо проверить исправность нагревательного элемента и выставить температуру соответствующую марке свариваемого полиэтилена.
Нерасплавленные углубления между торцами сваренных труб. Возможно, температура нагрева торцов труб была недостаточной или технологическая пауза (время извлечения нагревательного элемента и сведения труб) была слишком продолжительной.
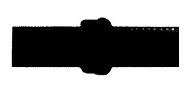
Сплющенный грат что это такое?
При анализе процесса отделения проката при помощи кислородной резки был выявлен существенный недостаток: образование грата значительного размера, образующегося из-за стекания и застывания расплавленного металла из зоны резания, образующийся грат при дальнейшем транспортировании его по роликам приводит к значительному их износу.
Цель исследования – повысить качество поверхности торца за счет устранения грата после газокислородной резки непрерывно-литых заготовок.
Анализ причин образования грата. В основе газокислородной резки лежит использование химического процесса сгорания металла в кислороде и физического процесса выдувания жидких окислов из полости реза. Концентрированный нагрев используется для доведения металла до температуры воспламенения в кислороде.
Основными параметрами газокислородной резки являются: мощность подогреваемого пламени, давление и чистота кислорода и скорость резки. Мощность подогревающего пламени определяется расходом горючего газа в единицу времени. В процессе резания необходимо обеспечить быстрый нагрев металла до температуры воспламенения, а также поддерживать процесс разрезания без оплавления кромок [1].
Расход кислорода должен обеспечивать интенсивное окисление металла и удаление из него продуктов сгорания. При недостатке кислорода появляется (так же как и при избыточной мощности подогревающего пламени) неотделимый грат на нижних кромках реза, вследствие того, что часть расплавленного металла в полости реза не окисляется и попадает в шлак, который по этой причине прочно приваривается к кромкам при вытекании. При избытке кислорода происходит охлаждение им металла, тепло выносится из зоны горения и нарушается процесс резки [2].
Повышение давления режущего кислорода приводит к увеличению скорости его истечения из сопла мундштука, что обеспечивает удаление шлаков с фронтальной поверхности полости реза, а следовательно, к улучшению условий для окисления металла. За счет повышения давления режущего кислорода скорость резки может быть повышенная в несколько раз, но для этого требуются аппаратура и трубопроводы трасс, рассчитанные на это давление, и применение мундштуков только с коническими соплами при очень высоком качестве обработки их внутренних поверхностей [3].
Мощность подогреваемого пламени определяется тепловой мощностью окисления и сгорания металла в струе кислорода, а также тепловой мощностью сгорания природного газа в кислороде. Сумма мощностей должна быть больше мощности, необходимой для расплавления металла; иначе будет снижаться качество, скорость и производительность кислородной резки [4].
Мощность необходимая на расплавление металла вычисляется по формуле:
где, ΔH – приращение энтальпии стали, при температурах близких к температуре плавления, и равно разности температурой плавления стали равной 14000С и температурой, при которой проводился эксперимент равной 8000С, которые для стали 40 соответственно равны Н1400=1,34*106 Дж/кг и H800=0,55*106 Дж/кг; ν – скорость движения резака, в эксперименте она равна 7,5*10-3м/с; h – ширина реза, в работе она равна 0,01 м; d – диаметр заготовки, он равняется 0,41 м; ρ – плотность стали, для стали 40 она равняется 7,8*103 кг/м3. Подставляя полученные значения в формулу (1), получим, что мощность, необходимая для расплавления металла, равна 187,5 кВт.
Мощность, необходимая на окисление и сгорание металла в струе кислорода (окисление Fe до Fe2O3), рассчитывается по формуле:
где, HFe2O3 – тепловой эффект горения металла, для стали 40 он равняется 196*103 кал/моль или 36,6*106 Дж/м3; QК – расход кислорода, в нашем случае он равен 0,06 м3/с;
γ – чистота кислорода, в данном эксперименте, она равна 97% или 0,97. Подставляя значения в формулу (2) получим, что Wок = 2,1*103Дж/с или 2,1 кВт.
Мощность, выделяемая при сгорании природного газа в кислороде:
где, Нпр – тепловой эффект горения природного газа в кислороде, его значение равно 33*106 Дж/м3; Qпр – расход природного газа, в нашем случае он равен 5*10-3 м3/с. Подставляя значения в формулу (3), получаем, что Wгор= 165 кВт.
Так как Wпл. должен быть Wок+ Wгор, (187,5 > 165+2,1 кВт), т.е. мощности кислородной резки недостаточно для полной расплавки металла, вследствие чего и происходит образование грата на торцевой поверхности заготовки. На рис. 1 показано образование грата на торце непрерывно-литой заготовки, после газокислородной резки.
Рис. 1. Образование грата на торце непрерывно-литой заготовки после кислородной резки
Практикой установленo [4], что использование кислорода чистотой ниже 97 % недопустимо, так как нарушается нормальное протекание процесса окисления, и образования разреза происходит за счет расплавления металла и выдувания неокисленного железа струей кислорода. Установлено, что наиболее целесообразно и экономически оправдано применение при машинной кислородной резке кислорода чистотой не менее 99,2 %. При этом уменьшение чистоты кислорода на 1 % снижает скорость резки в среднем на 20 % [5].
Так как на ОАО «ВТЗ» используется газокислородная резка с чистотой кислорода 98,4 % и 97 %, то это также является причиной образования грата.
Были проведено экспериментальное исследование влияния чистоты кислорода на размеры грата при разрезании непрывно-литых заготовок. На рисунке 2 представлена диаграмма параметров образующегося грата, в зависимости от чистоты режущего кислорода.
Рис. 2. Параметры грата при газокислородной резке, в зависимости от чистоты режущего кислорода
Вывод. В ходе проведения работы были выявлены причины появления грата на поверхности заготовки после кислородной резки. К ним относятся недостаточная мощность кислородной горелки, недостаточное давление кислорода в сопле и низкая чистота содержания режущего кислорода. Для устранения грата предлагается: повысить мощность энергии кислородной резки, за счет установки дополнительных горелок; повысить давление режущего кислорода, за счет применения мундштуков с коническими соплами; и увеличить чистоту режущего кислорода с 97 % до 99,5 %.
Рецензенты:
Полянчиков Ю.Н., д.т.н., профессор кафедры «Технология машиностроения» ФГБОУ ВПО «Волгоградский государственный технический университет», г. Волгоград;
Ханов Г.В., д.т.н., профессор, заведующий кафедры «Начертательная геометрия и компьютерная графика» ФГБОУ ВПО «Волгоградский государственный технический университет», г. Волгоград.
Как правильно применять станок для сварки ПНД труб, чтобы избежать брака
Полиэтилен низкого давления (ПНД) – базовое сырье для производства полимерных труб, применяемых в большинстве промышленных целей. Они востребованы в строительстве, жилищно-коммунальном хозяйстве, прокладке газо-нефтепроводов и так далее.
ПНД — термопластичный материал, выдерживающий многократные циклы нагрева-остывания без потери физических и химических свойств. Поэтому основными способами его соединения является сварка стыковым или электромуфтовым методом. Причем, для труб (толщиной стенки более 5 мм) предпочтительнее соединение встык. Если станок для сварки ПНД труб эксплуатируется правильно, то шов получается прочнее и надежнее самой трубы. Но, к сожалению, нередко сварщики допускают ошибки, вызывающие трещины и другие нарушения целостности трубопровода. Это приводит к утечке содержимого и может нанести большой финансовый и экологический урон.
По данным экспертов, брак при сварке в 80% случаев возникает из-за несоблюдения технологии. Еще около 18% – на совести производителей некачественных труб и фитингов, менее 2% — проблемы с оборудованием для сварки ПНД труб.
Что особо неприятно, почти половина дефектов возникает в самом начале, на этапе подготовки к пайке труб. Так, сварочная бригада в аврале может ненадлежащим образом выполнить зачистку торцов или не устранить загрязнения в зоне сварки.
В большинстве случаев неправильно сваренный шов легко выявить при визуальном осмотре. О том, как по виду «губы» понять причину и проделать работу над ошибками – читайте ниже.
1. Неравномерная высота грата
Шов внешне выглядит равномерным и симметричным, но при этом высота внутреннего и наружного грата местами различается на 50% и более (проверяется методами неразрушающего контроля, например, с помощью ультразвука).
Вероятная причина брака: некачественная обработка краев труб из-за чего образовался чрезмерный зазор между их торцами. По нормативам НАКС, торцевание стыков должно происходить до образования непрерывной ленты, примерно вдвое больше окружности трубы. Игнорирование этого правила приводит к браку. Увеличенный зазор может возникнуть также при слабом прижимном усилии во время соединения расплавленных изделий. На лицо «человеческий фактор», такой результат получится на любом, самом дорогом станке для сварки ПНД труб, если он оказался в руках у неквалифицированного работника.
2. Неравномерное распределение грата по шву
Шов может казаться ровным, но местами между валиками почти неразличима впадина, которая в норме легко заметна и располагается ровно посередине шва. Кроме того, грат имеет различную высоту в разных точках своего периметра и более 50% — в диаметрально противоположных точках. Например, в верхней части трубопровода валики грата будут высотой 10 мм, а в нижней – 4 мм. При этом внутренний грат местами также будет иметь увеличенную высоту (это определяется в ходе дефектоскопии) и станет барьером при движении жидкостей и газов по трубопроводу. В этом месте возможно скопление отложений, приводящее к закупорке и сбоям транспортировки сырья.
Причина: на этапе прогрева труб произошло смещение нагревательного зеркала. Такое случается при использовании механических станков для сварки ПНД труб начинающими или невнимательными сварщиками.
3. Частичная асимметрия грата
Если валики грата разнятся по высоте на 40% и более и одна из сваренных труб кажется приподнятой (визуально заметна «ступенька» в месте стыка) – налицо еще одна распространенная ошибка. По вине сварщиков произошло смещение изделий в центраторе из-за недостаточно жесткой фиксации. Вероятно, выбраны неподходящие редукционные вкладыши или скривилась станина центратора. Увы, такой сюрприз могут устроить товары недобросовестных производителей, даже если варится трубопровод средних диаметров 110-350 мм. В то же время, даже самый качественный станок для сварки ПНД труб больших диаметров (500-1500 мм) нужно «подстраховывать» дополнительными подпорками у свободных концов труб. Это увеличит срок службы прибора и гарантирует симметрию грата.
4. Асимметрия валиков грата по окружности стыка
В случае, когда один валик грата заметно выше или ниже соседнего на всем протяжении шва (то есть по всей спаянной окружности) можно предположить такое нарушение, как подбор разносортных труб. То есть по недосмотру снабженцев или сварочной бригады произведена попытка соединить встык трубы из различных материалов, разных диаметров или толщины стенок. Такое допустимо в случае муфтовой сварки, когда «разносортица» нивелируется фитингами. Но стыковая сварка полиэтиленовых труб применима только к абсолютно одинаковым изделиям. Поэтому прежде, чем закреплять трубы и приступать к нагреву, нужно всегда сверять их маркировку. Проверка идентичности маркировки на изделиях занимает пару минут, а экономит часы работы и тонну нервов.
5. Малый или большой грат округлой формы
Если высота наружного грата меньше или больше допустимых нормативом значений, это указывает на неверно выбранное время и температуру прогрева. Так, малый грат свидетельствует о том, что сварщик поторопился, не выдержав положенное время и/или применил недостаточное давление при осадке шва. Увеличенный грат напротив – показывает, что нагреватель касался полиэтилена слишком долго и к тому же, вероятно, был нагрет больше положенного.
Шов может иметь другие отклонения. Например, он покрыт многочисленными пузырями, «раковинами» и другими неровностями, нередко имеющими следы растрескивания. Это говорит о том, что температура нагревания существенно превысила рекомендованную для данного вида полиэтилена и привела к деструкции изделия. То есть вследствие «агрессивной» сварки полимер потерял часть своих физико-химических свойств, изменил молекулярную структуру и стал ломким.
Устранить это и ряд вышеописанных нарушений можно лишь распилив трубопровод с обеих сторон от шва и сварив его заново, но уже четко следуя инструкциям.
Таким образом, используя механический или полуавтоматический станок для сварки ПНД труб, тщательно сверяйте маркировку, очищайте торцевые и прилегающие поверхности, подбирайте правильные редукционные полукольца, следите за температурой, давлением и временем прижатия. Это обеспечит надежный, ровный и качественный шов, отвечающий всем техническим требованиям.
Для больших объемов работ и на особо ответственных участках (к ним относятся, например, газо-нефтепроводы) рекомендуется применять полностью автоматические сварочные аппараты для ПНД труб, купить которые можно прямо на нашем сайте.
Трубы электросварные круглые
К данной группе относятся стальные электросварные прямошовные трубы из углеродистой и низколегированной стали, применяемые для трубопроводов и конструкций различного назначения.
Существует много видов электросварных прямошовных труб, в том числе:
- круглые;
- профильные (квадратные, прямоугольные, овальные);
- профили стальные гнутые замкнутые сварные (квадратные и прямоугольные).
К данной группе относятся стальные электросварные прямошовные трубы диаметром:
от 10 до 530мм по ГОСТ 10705-91 (заменяет ГОСТ 10705-80);
от 478 до 1420мм по ГОСТ 10706-76.
Сортамент труб соответствует ГОСТ 10704-91 (заменяет ГОСТ 10704-76)
По длине трубы изготовляют:
немерной длины от 2 до 12м;
мерной длины от 5 до 12м;
Трубы диаметром свыше 426мм изготовляют только немерной длины
Трубы мерной и кратной длины изготовляют двух классов точности по длине:
с обрезкой концов и снятием заусенцев;
без заторцовки и снятия заусенцев (с порезкой в линии стана).
Трубы изготовляют из стали марок:
Ст2сп, Ст2пс, Ст2кп, Ст4сп, Ст4пс, Ст4кп по ГОСТ 380
10, 10пс, 20, 35, 45, 08кп по ГОСТ 1050.
В зависимости от показателей качества трубы изготовляют следующих групп:
А — с нормированием механических свойств;
Б — с нормированием химического состава;
В — с нормированием механических свойств и химического состава;
Д — с нормированием испытательного гидравлического давления.
Трубы изготовляют термически обработанными (по всему объему трубы или по сварному соединению), горячередуцированными и без термической обработки.
На трубах диаметром 57мм и более допускается один поперечный шов.
Трубы диаметром 820мм и более должны иметь два продольных и один поперечный шов.
Отличия ГОСТ 10704, 10705 и 10706
При изготовлении прямошовной трубы обращают внимание на ГОСТ 10704-91, который определяет сортамент, и ГОСТ 10705-80, а также ГОСТ 10706-76, основные технические требования для труб общего назначения. Двумя технологиями сварки определяется наличие двух ГОСТов, а именно электродуговая сварка и контактная сварка токами высокой частоты.
В ГОСТе 20295-85 разные сварочные технологии только упоминаются, но напрямую об этом нигде не говорится. Подразумевает контактную сварку токами высокой частоты ГОСТ 10705-80, причем распространяется на трубы диаметром 10-530 мм.
На трубы большого диаметра, от 428 до 1420 мм, изготовленные методом дуговой сварки, распространяется ГОСТ 10706-76. Электродуговая сварка проводится с внешним усилением, это значит, что труба сваривается в три захода: вначале – промежуточный шов, затем наружный, для усиления изготавливается внутренний шов. Эти два ГОСТа для прямошовных труб весьма похожи, но имеют существенные отличия.
Исходя из ГОСТа 10706 трубы небольшого диаметра могут быть сварены поперечным швом, а диаметром от 820 мм должны иметь два продольных и один поперечный швы. Еще он, в отличие от ГОСТа 10705, регламентирует фаску на торцах трубы. Есть и определенные различия касательно марок стали, допустимых при изготовлении труб. По ГОСТу 10706-76 допускается две основные марки, это СТ.3 и Ст.2, а вот ГОСТ 10705-80 уже не ограничивается двумя марками стали 10 и 20. Изготовление труб из марки стали 17ГС и ее аналогов по ГОСТ 10705-80 и 10706-76 не предусмотрено.
Визуальные характеристики шва от высокочастотной сварки значительно выше, чем от электродуговой, такой шов более узкий и практически незаметен. Неровности в виде негладкого утолщения в зоне шва образуются на внутренней поверхности трубы, именуются гратом. В некоторых случаях грат сплющивают или зашлифовывают, наружный удаляют. После электродуговой сварки шов более широкий. Его характеризуют наличием валика усиления с высотой до 5 мм, при этом с обеих сторон – внутренней и внешней.
Оборудование для удаления грата сварных труб
При сварке давлением происходит вытеснение избытков металла в грат на наружной и внутренней поверхности. Наличие грата ограничивает область применения электросварных труб, поэтому его удаление является одной из важных технологических операций.
Грат с наружной поверхности, как уже отмечалось, удаляется резцами, расположенными после сварочной клети. Более трудную задачу представляет удаление внутреннего грата из-за отсутствия контроля и технических трудностей размещения режущего инструмента.
Рис. 1. Гратосниматель конструкции АО «внииметмаш» для удаления внутреннего грата резцом в поточной линии ТЭСА
На рис. 1 приведена конструкция гратоснимателя для удаления внутреннего грата резцом, разработанного во ВНИИметмаше. Гратосниматель опирается на внутреннюю поверхность трубы роликом 7. Ось ролика закреплена в плунжере 2, который перемещайся в корпусе 3 и при срезании грата прижимает резец к внутренней поверхности трубы. Масло в рабочую полость цилиндра подайся через систему отверстий 4 в штанге гратоснимателя. При отключении гидравлики, пружины 5 выдавливают масло из рабочего Цилиндра и убирают нижний опорный ролик в корпус, в результате чего происходит опускание штанги. Резец 6 крепится к корпусу между верхними опорными роликами 7 и 8. Ролики ограничивают глубину внедрения резца в металл трубы, благодаря чему внутренний грат удаляется с высокой точностью. Ролик 8 снабжен звездочкой 9 для насечки грата.
Срезанный грат отводится от резца через направляющее окно 10 и затем удаляется из трубы. Корпус 3 жестко закреплен с ферритодержателем 11. Для уменьшения влияния штанги гратоснимателя на процесс нагрева кромок, ферритодержатель выполняется из немагнитной стали. В ферритодержателе имеется паз для ферритных колец 12, которые снижают потери мощности в сварочном трансформаторе. Это позволяет использовать гратосниматель для удаления внутреннего грата при сварке труб токами высокой частоты.
Штанга гратоснимателя крепится при помощи стойки одной из клетей формовочного стана с валками открытого калибра. Конструкция стойки позволяет перемещать штангу гратоснимателя в горизонтальном и вертикальном направлениях. Механизм крепления оборудован устройством для поворота штанги в обе стороны относительно шва при любых смещениях. Средняя стойкость резца гратоснимателя составляет 2 ч. Для смены резца стан останавливают, в трубе автогенным резаком вырезают окно и заменяют изношенный резец. На смену резца затрачивают 5-6 мин. Вес всего оборудования составляет 150 кг. Такой гратосниматель не снижает скорость сварки труб, прост и надежен в эксплуатации, для его обслуживания не требуется дополнительного персонала.
Удаление внутреннего грата резцом осуществляется не только в линии трубоэлектросварочных станов, но и на специально разработанном для этой цели оборудовании.
Производительность установок для удаления внутреннего грата вне потока станов составляет 250 — 300 м/ч, в то время как производительность современных трубоэлектросварочных станов 3000 — 4000 м/ч. Поэтому для обработки труб, сваренных на одном стане, необходимо иметь 10 установок для снятия внутреннего грата. Установки для удаления грата вне линии стана занимают много места, для их обслуживания необходим дополнительный персонал. Вес оборудования установок составляет 20 — 30 т.
Кислородный гратосниматель (рис. 2) предназначен для сжигания внутреннего грата в процессе сварки труб и устанавливается в потоке трубоэлектросварочных станов, состоит из штанги U головки 2, сменных сопел 3 и прижимного механизма. Штанга гратоснимателя представляет собой две трубки, расположенные одна в другой. По внутренней трубке 4 подают кислород, по трубке циркулирует вода, охлаждающая штангу и головку гратоснимателя. Головка выполнена в виде вилки из двух нержавеющих трубок, на концах которых имеются штуцеры для крепления сменных сопел. Зазор рис. 2. кислородный гратосниматель между соплами и внутренней стенкой трубы обеспечивается роликовым упором 6.
Рис. 2. кислородный гратосниматель
В нижней части штанги расположен прижимной механизм, состоящий из пластинчатой пружины 7, рычага 8 и роликовой опоры 9.
Во избежание перегрева прижимное устройство выносится из зоны сварки в сторону формовочного стана на расстояние 100 — 150 мм от оси сварочных валков. Струя кислорода, подаваемого из двух сопел, направлена навстречу движению трубной заготовки под углом 60°. Сопла гратоснимателя находятся на расстоянии 80 — 100 мм от очага сварки, где температура составляет 1300 — 1400 °С. Под действием струи кислорода и высокой температуры грат сгорает. Для обеспечения равномерного сжигания необходимо, чтобы скорость сгорания грата соответствовала скорости сварки трубы. При недостатке кислорода происходит неполное сгорание грата, а при его избытке — окисление сжигаемого металла, что нарушает процесс горения. Недостатком этой установки является то, что капли металла, образующиеся в процессе сварки, даже при обильном охлаждении налипают на штангу, вследствие чего головку заклинивает и она часто выходит из строя. Это усложняет процесс производства труб и не обеспечивает стабильное удаление внутреннего грата.
Удаление внутреннего грата электроэрозионным способом осуществляется вне линии стана на специальных установках. Сущность этого способа основана на том, что между двумя электродами, подключенными к источнику питания, возникает мощный электрический разряд, в результате чего металл в виде мелких частиц выбрасывается с поверхности электродов. В месте выброса металлов образуется лунка, размеры которой зависят от степени развития дугового процесса, мощности и частоты импульсов. Процесс происходит в жидкой среде: масле, керосине, воде, жидком стекле. Среда выбирается в зависимости от мощности разряда и источника питания.
Установка для удаления внутреннего грата электроэрозионным способом характеризуется малой производительностью, нестабильностью процесса и высоким износом инструмента.
Для удаления внутреннею грата существует также электролитический способ. Внутрь трубы под давлением 1-2 МПа подается раствор поваренной соли и вводится стержень — катод. Труба является вторым электродом — анодом. Между трубой и стержнем пропускается электрический ток, при этом происходит растворение внутреннего грата. Процесс электролитического удаления грата нетехнологичен и характеризуется малой скоростью (0,15 — 0,2 м/мин).
Способы удаления грата путем деформирования. Одним из таких способов является закатка внутреннего грата.
Рис. 3. Роликовая головка для закатки внутреннего грата
Закатка производится в линии трубоэлектросварочных станов роликовой головкой (рис. 3). Головка представляет собой массивный корпус 7, в котором жестко закреплены верхний закатывающий ролик 2 и два нижних опорных ролика 3. Корпус соединен штифтом 4 с тягой 5, которая, в свою очередь, при помощи стойки неподвижно закреплена на станине рабочей клети формовочного стана. Закатку грата производят верхним рабочим роликом, нижние ролики являются опорными и катятся по внутренней поверхности трубы. Перед эксплуатацией ролики головки выставляются по шаблону с таким расчетом, чтобы расстояние между нижними опорными и верхним раскатывающим роликом равнялось внутреннему диаметру трубы с плюсовым допуском. Корпус раскатывающей головки располагается внутри трубы так, чтобы ось рабочего ролика находилась в одной плоскости с осями роликов гладильной клети.
Раскатка производится при температуре шва 500 — 600 °С. В этом интервале температур грат обладает еще достаточной пластичностью. Раскатка грата при более высоких температурах вблизи зоны сварки приводит к налипанию капель расплавленного металла на ролики, вследствие чего происходит их заклинивание. При установке гратозакатывающей головки на значительном расстоянии от зоны сварки при более низких температурах остывший грат вдавливается в сварной шов, что приводит к образованию микротрещин.
В связи с большими нагрузками и высокой температурой создаются тяжелые условия работы подшипников рабочих и опорных роликов. Продолжительность их работы составляет 40 — 60 мин, а при раскатке грата в трубах, к качеству которых предъявляют повышенные требования, не более 20 — 30 мин. Помимо низкой стойкости не обеспечивается качественная обработка труб: грат закатывается неравномерно, высота остатка грата превышает 0,5 мм и изменяется по длине трубы. Кроме того, труба с закатанным гратом отличается пониженной прочностью сварного соединения и источником повышенной коррозии.
Другой разновидностью гратозакатывающего устройства является вибрационная установка.
Внутренний грат забивается бочкообразным бойком, совершающим колебательное движение. Вибрационное устройство устанавливают на станине формовочного стана таким образом, чтобы боек располагался за осью шовсжимающих роликов на расстоянии 50 — 60 мм. В этой зоне грат имеет температуру 1300 — 1350 °С, при которой обладает высокой пластичностью. Под ударами бойка грат пластически деформируется заподлицо с внутренней поверхностью обрабатываемой трубы.
Вибрационная установка по сравнению с установкой для закатки грата роликом, имеет более сложную конструкцию и менее равномерно закатывает грат. Кроме того, вибрационная установка требует тщательной настройки, сложна в эксплуатации и не обеспечивает равномерной деформации внутреннего грата по длине трубы.
Предотвращение образования внутреннего грата в процессе производства труб. Изыскание способов производства высококачественных электросварных труб без внутреннего грата не ограничивалось исследованием возможностей установок для удаления и деформирования внутреннего грата. Ряд работ был направлен по пути создания технологии производства электросварных труб без внутреннего грата.
Существует несколько способов производства труб без внутреннего грата. Конструкция устройства (рис. 4), предотвращающего разование внутреннего грата с помощью подкладки, состоит из ственно подкладки 1, закрепленной во вкладыше 2, который под действием набора пластинчатых пружин 3 перемещается в пазу корпуса 4 и прижимает подкладку к трубе в месте формообразования шва. Корпус жестко соединен со штангой 5, которая закреплена на одной из станин рабочей клети формовочного стана. Штанга может перемещаться в горизонтальном, вертикальном и радиальном направлениях.
Рис. 4. Устройство для предотвращения образования грата с помощью подкладки
Внутри штанги проходят каналы, по которым подается вода для охлаждения подкладки, корпуса и пружин.
Данное устройство предотвращает выдавливание грата внутрь трубы во время сварки.
Рис. 5. Сопло для газового подпора
Для предотвращения внутреннего грата в трубах, сваренных в среде инертных газов, применяют газовый подпор, при котором в зоне сварки под сварочной ванночкой создается давление инертного газа, препятствующее провисанию жидкого металла, т. е. предотвращающее образование внутреннего грата. В качестве инертного газа используется аргон. Газовый подпор создается соплом, установленным внутри трубы (5).
Сопло 1 (из меди или латуни) приваривается к газоподводящей трубе 2 с продольной регулировкой для установки его на различном расстоянии от электродов. Для создания эффективного газового подпора утечка газа должна быть минимальной. К недостаткам метода газового подпора относятся: образование внутренней пористости и строчечности шва, неустойчивость процесса и дополнительный расход аргона.